Virginia organ builder Taylor & Boody
Paul Hale
Friday, February 21, 2025
Paul Hale considers the work of the Virginia organ builder Taylor & Boody, whose historically informed practice also satisfies modern demands
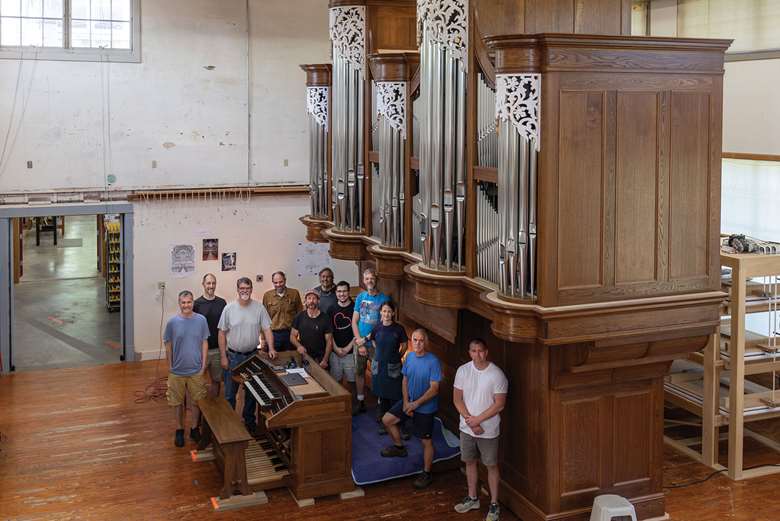
In the United States, one of the earliest advocates of the re-introduction of mechanical action, coupled with detailed study of the finest historic organs, was the organ builder John Brombaugh, whose first instruments were made in the late 1960s. Absolutely the right man at the right time, Brombaugh drew into his Ohio workshop a group of talented disciples and partners, many of whom later set up on their own account. This helped establish a solid body of organ builders inspired by historical organs – their techniques of construction, their appearance and their sound – all of whom had the vision, the determination and, not least, the courage, to pursue a path away from the eclecticism of the ‘American Classic’ organ, seeking to build instruments founded on historical tradition.
Among those who worked with Brombaugh (including in the 1970s when several of his seminal organs were built) were well-known figures such as Paul Fritts, Michael Bigelow, Charles Ruggles, Bruce Fowkes, David Petty, George Taylor and John Boody. There they learnt about hammered lead for pipes, unequal temperaments, making reed pipes according to historic patterns, the use of solid wood rather than ply in cases and soundboards, the appropriateness of wedge bellows, case design according to historic principles, and to voice pipes in a singing ‘vocale’ manner.
Penny, the workshop cat, inspects façade pipes
In 1977, George Taylor and John Boody left Brombaugh, where they had been his business partners, to set up by themselves, in 1979 establishing their current workshops in spacious former school buildings in undulating Virginia countryside near Staunton. Since then, the firm has made more than 80 instruments, for churches, schools and private practice. This article looks at their most recent work and considers how their style has developed since the heady early days of the tracker revival, into the rather different organ world of today, where students are more likely to reach for Vierne than Buxtehude.
Completed in 2023 was a comprehensive 2-manual, 34-stop (plus 2 derivations) instrument for Ancilla Domini Chapel, Plymouth, Indiana, the company’s Op 83. This instrument owes much to the early work of the firm, in that it is in North German style, with complete flue and reed choruses on Hauptwerk, Oberwerk and Pedal, there being two 16ft flues on the Hauptwerk (the 16ft Principal drawing also on the Pedal), a 16ft reed on both Hauptwerk and Oberwerk, and an impressive chorus of Pedal reeds at 32.16.8.2, plus the transmission of the Great 16ft Trompet. There is a Cornet on the Great and a narrow-scale Sesquialtera on the Oberwerk. There are no fewer than 11 independent 8ft stops to give variety and richness, though no 8ft flute on the Pedal, which does limit Pedal independence in soft music such as chorale preludes and trios. However, a careful look at the stop list will reveal a close resemblance to the much larger 1693 Arp Schnitger in Hamburg’s Hauptkirche St Jacobi; and guess what – no secondary Pedal 8ft there either.
The firm describes Op 83: ‘Enclosed in a free-standing, solid-wood case, the Hauptwerk division speaks from impost level, and the Oberwerk from directly above that. The Pedal is similarly on two levels behind the main case, with wide walkboards in between. Wind is provided by three large wedge bellows, feeding a common wind trunk which in turn supplies the same pressure (80mm) for all divisions. The stop action is completely mechanical, though it can also be operated by solenoids and a combination action.’ The temperament is gently unequal and the pitch is, usefully, a=440Hz.
Joel VanderZee casts pipe metal
A further instrument, Op 85, was finished during 2024. Designed for Christ Church, New Bern, North Carolina, this II/26 organ is more typical of the style the firm is asked for today. Despite taking up relatively little space in the west gallery, it still has complete flue choruses in all three departments, plus four reeds (two of which are also derived to the Pedal), ensuring an impressive tutti. The firm explains: ‘Where the organ differs from our work of the past is in the refinement of the speech of the choruses, the expressive enclosure of the complete Swell division, and the Great and Swell strings, which take inspiration more from American examples of the last century than from 18th-century Germany.’ Sensibly, alongside its sensitive mechanical key action, it has an electric stop action and the now customary console equipment so necessary for flexible and colourful liturgical and solo use. There is a detached console, set back to the gallery rail, allowing better sightlines to the choir. Space is saved within the base of the organ by situating the blower and bellows in a climate-controlled room behind the instrument.
An exciting project for Taylor & Boody is the current instrument under construction, a 71-stop 4-manual for Luther Memorial Church, Madison, Wisconsin. The specification is worthy of study.
Joel VanderZee takes up the story: ‘Op 88 pushes the limits for us not just tonally, but mechanically as well. In a gallery framing either side of a stained-glass window it is an organ within an organ: an independent, mechanical-action organ in the east case, with Great, Positive and Pedal controlled by a console built into the case; in the west case are a Swell, Solo and Solo Pedal on electric slider chests, controlled by a central console, which will be capable of playing the entire organ. The Swell and Solo will both be enclosed and expressive. The size of the organ allows a specification with few compromises, and allows us to make some stops that are infrequent or new to us, like the Great 8ft Doppel Gedackt, the Tannenberg inspired Flauta Amabile 8 and its Celeste partner on the Solo, and a full-length 32ft Posaune made of solid wood in the Pedal. Installation of the organ will be in two phases: the tracker (East) organ is scheduled to deliver in early 2026, with the electric console and West organ coming in 2027.’
These three instruments vividly proclaim the variety of styles to which the company’s underlying principles can be applied. Taylor & Boody concludes: ‘Throughout our history we have valued the clear singing principal choruses that provide sweet and present congregational pitch integrity, as well as warm foundations and pedal reeds for rhythmic reinforcement. Clarity and sweetness are paramount, not only for polyphony, but to be a model of good chorister vowel tone and consonant crispness. Add to this base sweet and bright flutes, warm and gentle strings, foundational and colourful reeds, and one can see an intension of honouring tradition while endeavouring to tailor each instrument to its space and programme.’
Nothing could be better evidence of this set of values than these three organ projects. It’s quite clear that under its new leadership, Taylor & Boody is far from resting on its laurels: it aims to win fresh approval for all that is to come.
Embracing sustainability
George Taylor, a graduate of Washington and Lee University, won a Ford Foundation award to serve an apprenticeship with Rudolph von Beckerath in Hamburg, Germany. At the time, Beckerath was one of the leading historically-informed firms in Germany, having undertaken much post-war restoration of damaged organs, as well as building new tracker instruments. Along with Rieger and Flentrop, Beckerath exported several organs to the United States. A seminal instrument of 1962 was installed in St Paul’s Cathedral, Pittsburgh, Pennsylvania. This, the first mechanical-action organ to be installed in a North American cathedral in the 20th century, proved a prophetic voice, preparing the way for Beckerath’s equally grand instrument in St Joseph’s Oratory, Montreal. An apprenticeship with Beckerath must have been very appealing for the young George Taylor. John Boody, on the other hand, stayed closer to home and having studied Forestry and Music was apprenticed to Fritz Noack in Georgetown, Massachusetts. Working with Noack may not have been all that different (except in terms of scale) to John Boody’s experience, as Noack had himself trained at Beckerath before arriving in the USA.
Clearly, with this background and some seven years in partnership with Brombaugh, Taylor and Boody were in a better position than most ‘start-ups’. Their hard-won abilities extended to being able – and keen – to make virtually all parts of their organs themselves, eschewing standard trade-supply parts.
In addition to its new instruments, the company has over the decades also carried out museum-quality restorations of significant historic organs including the 1800 David Tannenberg organ from the Home Moravian Church in Salem, North Carolina. As they have written: ‘The knowledge and practice gained through restorations, and the study of numerous antiques both here and abroad, has influenced the firm in building new organs in distinctive historical styles. These include a three-manual meantone organ in North German Baroque style for the Yale Institute of Sacred Music and the Tannenberg-inspired organ for the First Presbyterian Church in Pittsford, New York.’
In 2005 the firm extended their buildings, to incorporate a new wood mill and a new pipe shop, where pipes are made from metal cast in a dedicated casting room. In 2018 a switch was made to solar energy. The firm comments: ‘This was achieved by mounting 109 solar panels on the flat, south-facing roof of our shop. Three inverters change the direct current to alternating current. The average annual output of the system is estimated at 46,251Kwh, which is sufficient to cover 100 percent of our demand.’
There is a fully equipped sawmill, located about five miles away. This means that the firm can, when desired, deal with complete trees. They explain: ‘For example, The Center at Donaldson in Plymouth, Indiana, had a large basswood tree on the property that was leaning over a parking area and needed to come down. They were able to send us the basswood trunk and two poplar trees from their property. John Boody sawed and dried them, and we made all of the carvings for Op 83 out of the basswood, and some of the internal structures out of the poplar.’
After 44 years of being in charge at Taylor & Boody Organ Builders, George and John officially retired in 2022. Their responsibilities were assumed by three of the most experienced members of the team’s younger generation – Erik Boody, Aaron Reichert and Robbie Lawson. The full team today comprises 12 workers, skilled in all facets of creating fine organs.
Paul Hale has written extensively about organs while also working as a cathedral organist, teacher and organ consultant